Six-sided Drilling Solution
Overview
- Overview
- Features and Benefits
- Related Products
- Related Cases
- Related News & Events
- Related Solutions
- Contact us
Six-sided Drilling Solution
In the production and processing of panel furniture such as wardrobes, cabinets, and planks, drilling, grooving and other processes are inseparable. At present, there are a variety of CNC drilling equipment in the industry, which can realize double-sided, four-sided and six-sided drilling. During the processing of the existing CNC six-sided drilling, only two clamping jaws are needed to complete the work of pressing, feeding, processing positioning, and discharging. When machining long workpieces, since the plates are often bent and unequal, in order to ensure the accuracy of vertical drilling and horizontal drilling, the two fixtures need to maintain a certain distance from the machining tool during the machining process. To complete the processing of long plate workpieces, it is necessary to switch the clamping jaws and adjust the clamping position multiple times, which will cause cumulative errors in feed and processing positioning.
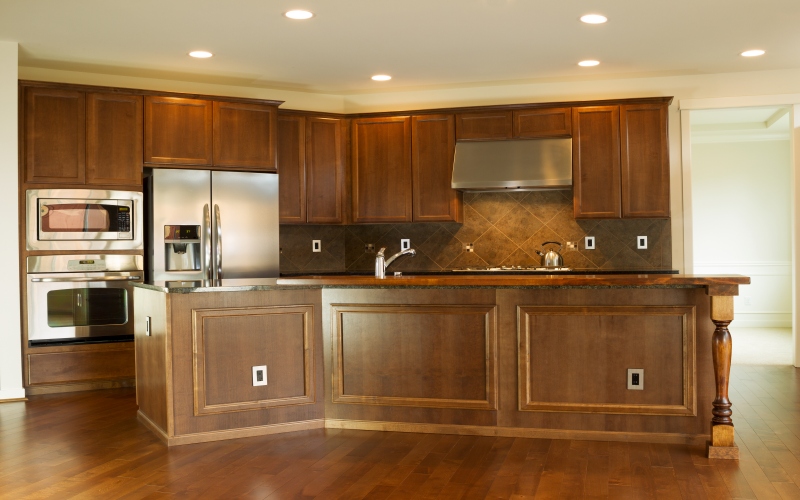
Features and Benefits
Industry introduction
Six-sided drills are mainly used in the drilling and processing applications of various man-made panels, solid wood panels, and semi-solid wood panels. It is a kind of numerical control processing equipment, which is easy to operate and fast in drilling and processing speed. It is suitable for all kinds of cabinet boards and other board furniture. As comprehensive drilling equipment, CNC five-six-sided drill is easy to operate, highly automated, efficient, and precise. It is professional equipment for drilling, grooving, and milling. Complete the processing of six face positions at one time, realizing high-efficiency and high-precision processing.
System topology
Program highlights
1. Using the bus control scheme, the PLC does not need to send pulses to control the servo, which simplifies the wiring and enhances the transparency of the system and the anti-interference ability of the system.
2. The servo drive has fast response, accurate positioning, stable operation, and all indexes of the finished product meet the requirements.
3. A dedicated servo motor is used to make the load operation more stable and accurate, and to ensure the accuracy of the hole position.
Process principle
Make the controller system and the servo drive realize the requirement of a six-sided opening. It adopts M2, M3, or EtherCAT bus control, faster communication speed, multi-axis linkage, good responsiveness, and simple wiring. The system supports CAM software to convert pictures into G codes and send them to PLC, and PLC will make corresponding curve planning.
Technical index
The machining accuracy can reach ±0.05mm.
The maximum processing speed is 12-25m/min.
Process 6 sides at a time.
Application