Electric Blow Molding Machine Solution
Overview
- Overview
- Features and Benefits
- Related Products
- Related Cases
- Related News & Events
- Related Solutions
- Contact us
Electric Blow Molding Machine Solution
In recent years, with the rapid development of my country's packaging industry, the market demand for various types of high-quality plastic filling bottles has continued to grow, and domestic filling bottle manufacturers have increasingly increased requirements for the automation and intelligent upgrade of the control system of the PET blow molding machine. For the traditional hydraulic blow molding machine equipment, there are problems such as slow running speed and inaccurate positioning. Based on market demand and combined with industry pain points, VEICHI has launched a full-servo electric blow molding machine system solution with high efficiency, strong stability, and diverse functions. It effectively improves the automation and intelligence level of the blow molding machine control system.
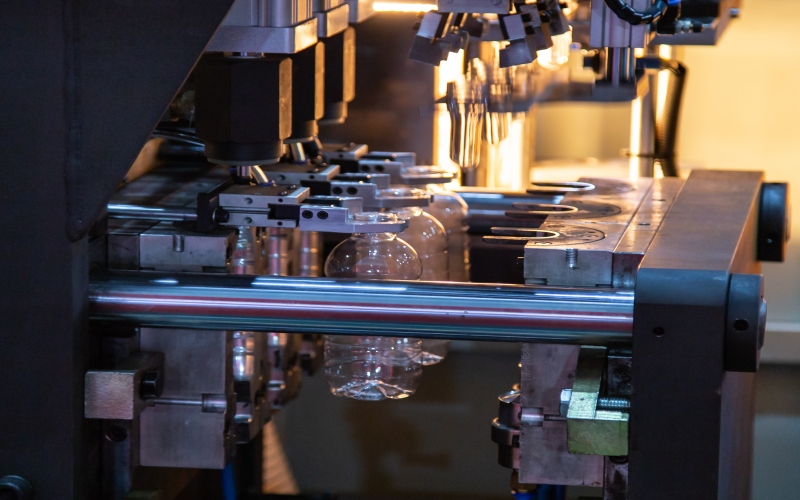
Features and Benefits
For the traditional hydraulic blow molding machine equipment, there are problems such as slow running speed and inaccurate positioning. Based on market demand and combined with industry pain points, VEICHI has launched a full-servo electric blow molding machine system solution with high efficiency, strong stability, and diverse functions. It effectively improves the automation and intelligence level of the blow molding machine control system.
Technology upgrade, precise and efficient
The entire control system of the whole servo electric blow molding machine system solution uses the self-developed products of VEICHI. Including PLC controller, servo driver, inverter, servo motor, etc. From the control layer to the execution layer, it can meet the production needs of different customers.
The solution control system adopts the VC3 controller of VEICHI, which calibrates the position in real-time through full pulse output to ensure that each filling position is consistent and has no offset. The blowing end servo uses the position plus torque mode to achieve uniform pressure on the bottle mouth under the premise of accurate position and fast speed. The hydraulic end uses terminals to trigger multi-speed, which fully meets the customer's requirements for the precision and stability of the die. Adjustable software and hardware filtering, and strong anti-interference ability, so that the system can play the best control effect in various environments.
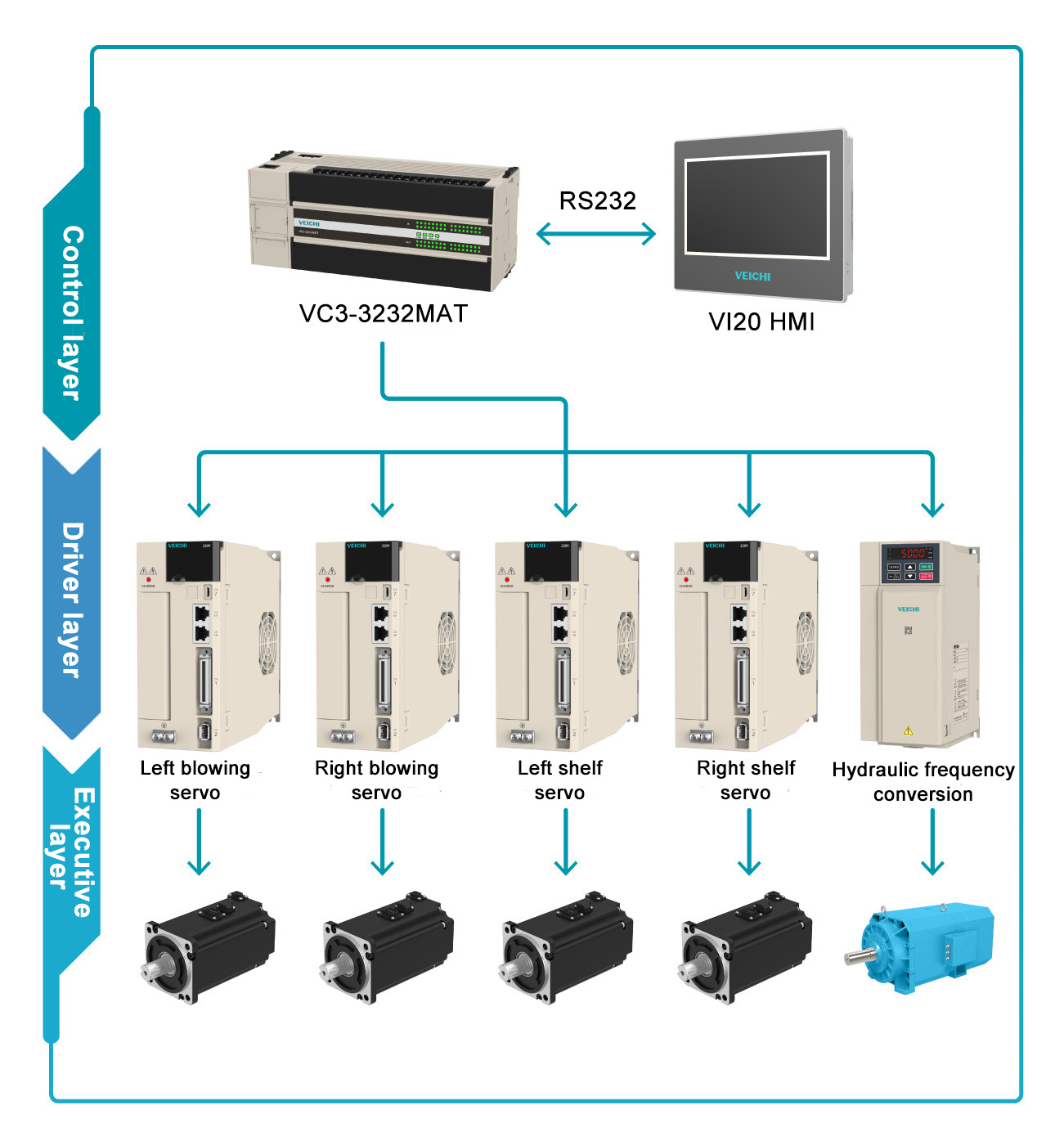
System topology
Three advantages, convenient and reliable
Independent research and development, efficient cooperation
The core components of the entire system solution are all VEICHI high-performance automation products to ensure PLC controllers, servo drives, frequency converters, touch screens, etc. It can achieve higher compatibility and stability, and at the same time can provide customers with more flexible solution options and timely and effective after-sales service.
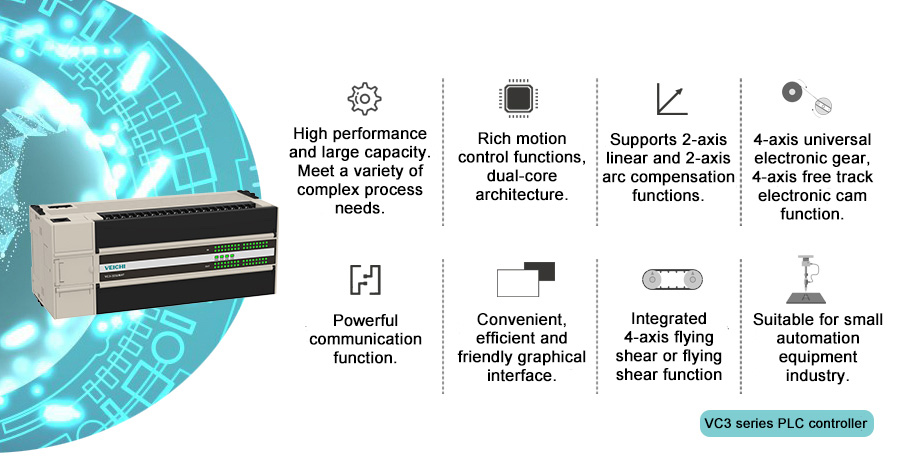
VC3 series PLC
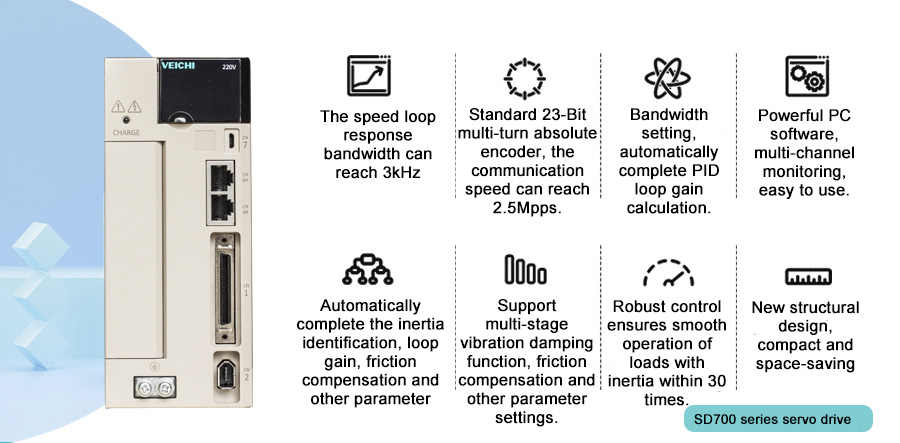
SD700 servo drive
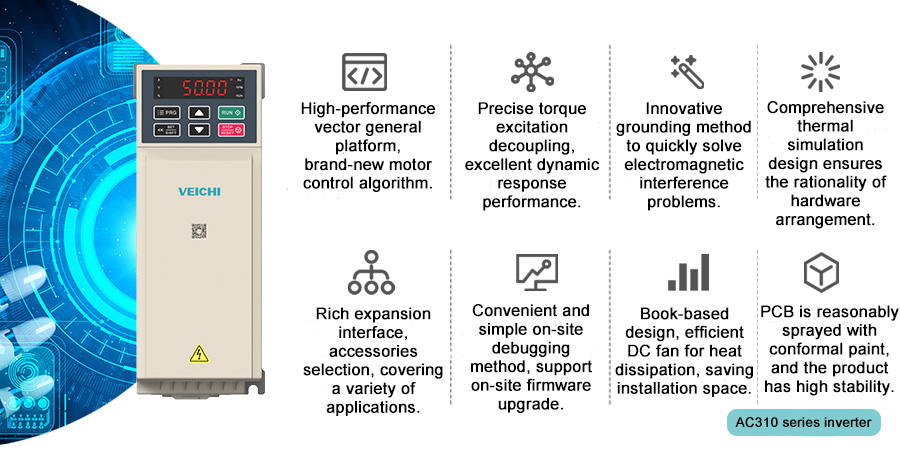
AC310 frequency inverter
Simple debugging and precise control
The scheme is equipped with a debugging mode for manufacturers to carry out pre-factory debugging to ensure zero problems at the customer site. Double racks and single racks can be selectively opened and closed, improving equipment flexibility. The use of interruptions to accurately measure the single cycle time, combined with the blanking time, makes the specifications of the molding materials highly consistent and improves the consistency of the products.
Fault self-check, parameter protection
The system is equipped with a fault self-detection function, including fault information of the servo variable frequency drive and fault solutions. At the same time, it also includes the fault shutdown function of the program logic, including the error reminder of parameter setting and the limit of the setting range, so as to avoid equipment damage caused by misoperation.
Relying on rich industry application experience and profound technical research and development advantages, VEICHI will further strengthen technology research and development and innovation in various industry application fields in the future while helping the intelligent transformation and upgrading of traditional packaging equipment. Deeply combine usage scenarios with product technology to continuously create value for customers.