- Home
- Product Launches
- Born for Enhancing the Positioning Efficiency of Machine Tool Spindle - AC200-CS
Overview
Since the announcement of VEICHI AC200 general-purpose frequency inverter, it has greatly improved the drive system efficiency for our customers with its excellent performance and excellent reliability. On the basis of high-performance closed-loop vector control of AC200, VEICHI AC200-CS integrates high-precision positioning technology, integrating speed control, position control and torque control into one as an organic whole, and it achieves closed-loop servo control of spindle motor. As the main drive system of the machine tool, AC200-CS spindle servo drive can achieve high-precision milling, turning, grinding and other processing, providing customers with a great variety of efficient machine tool processing solutions.
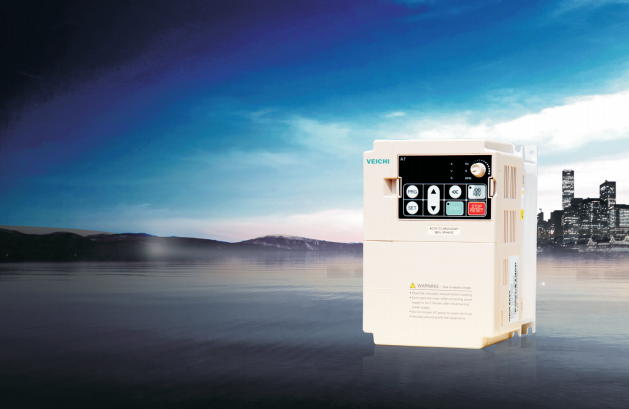
VEICHI AC200
System Program
In this article, we mainly introduce the application of the AC200-CS spindle servo drive on the lathe spindle. As the spindle driving unit, AC200-CS cooperates with the CNC system's command, implementing spindle speed adjustment and positioning, and completing the operation of rigid tapping.
System architecture diagram
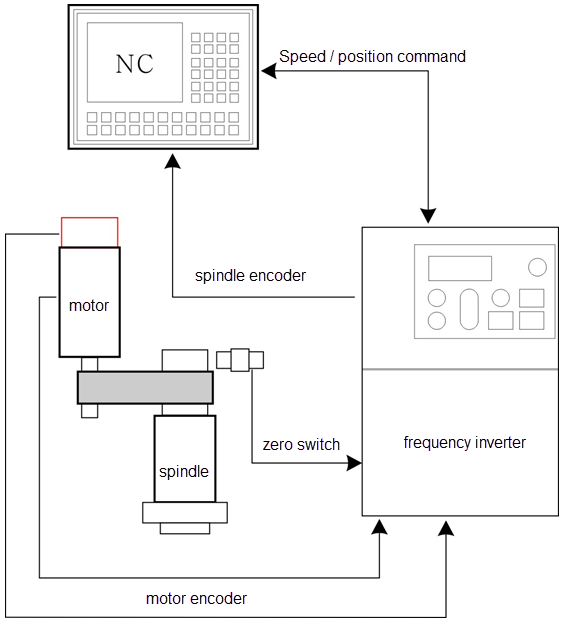
System architecture diagram
Processing flow and operation steps
(1) Before running, manually rotate the spindle, adjust the spindle position to the set position, query the drive parameter C-40 (spindle current angle), and enter the parameter value to parameter F9-37 manually.
(2) Start the machine tool, install the fixture and lock the chuck. Input M03 or M04 (spindle positive/negative run command), adjust the speed through the analog signal, then the spindle goes into high-speed rotation and turning goes to the station for turning.
(3) When the turning process is completed, the CNC system gives the M19 (spindle positioning) command, the spindle will rotate to the set angle.
(4) When the workpiece turns to the set angle, the CNC machine will give M29 (rigid tapping) command; spindle will follow the pulse number given by the machine tool, until the workpiece is completed.
(5) After the processing is completed, chuck releases and machine tool shuts down.
AC200-CS Features
Performance
A. low frequency rigidity:
It can output 180% of the rated torque at 0.5Hz, ensuring high stability and reliability of machine tool workpiece at low speed. In the zero servo state and the condition of the rated load, the fastest response can be completed within 50ms, and ensure that the spindle is always in the stopped state.
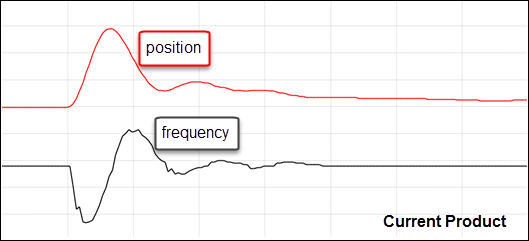
Current product
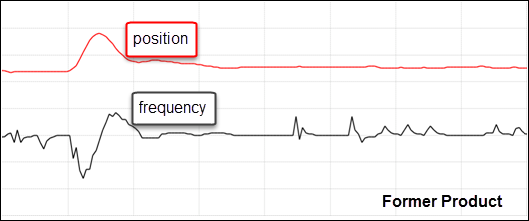
Former product
B. speed, position response upgrade:
AC200-CS spindle servo drive combines voltage& current suppression and dynamic braking, which makes the machine tool drive unit (spindle) can achieve acceleration and deceleration quickly and steadily, improving production efficiency. In the position mode, the loop adjustment cycle is greatly improved to ensure that the spindle can quickly make a position response and quickly complete the positioning control.
At the same conditions, the motor deceleration time is reduced to the original 1/2 or more, the spindle quickly and accurately slow down, safe and reliable.
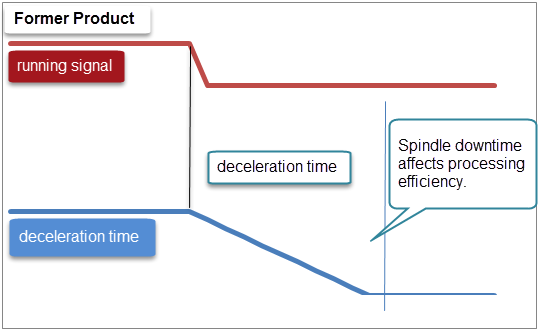
former product deceleration time
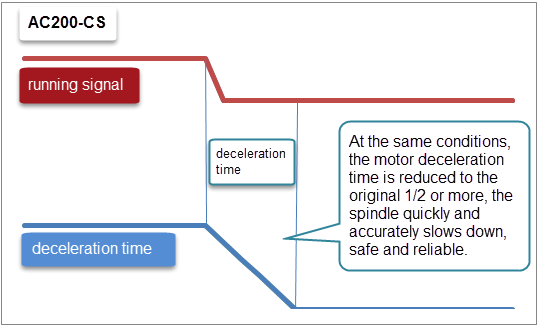
AC200-CS deceleration time
C. Large torque at low frequency, strong weak magnetic field ability
It can meet the spindle's precision machining above 5000rpm, but also can meet the rigid tapping below 40rpm.
Strong applicability
It is applicable to all kinds of CNC machine tools, capable of driving CNC milling machine, CNC lathes, CNC boring machine, CNC grinding machine, spindle and others.
It can adapt AC servo spindle motor, variable frequency motor, three-phase asynchronous motor.
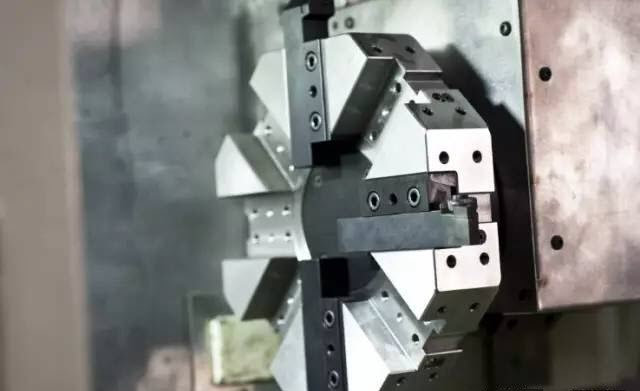
CNC machine tools
Characteristic application
8-segment spindle quasi-stop indexing control: the accurate stop accuracy of reaming workpiece processing can be accurate to 0.1° or less at the positioning condition of continuous multi-axis, 360 ° arbitrary angular position, continuous 8-position positioning.
Rigid tapping: support pulse + direction, AB orthogonal pulse input command, the maximum speed of rigid tapping can reach 5000 rpm, tapping error within ± 1 pulse.
4-segment internal multi-segment position: the internal position command parameter of each section is set independently, single or multi-segment position can be cyclically positioned to facilitate the user to plan the trajectory of the spindle.
Origin return: ensure automatical return to the set origin after workpiece is completed each time. The zero switch can be installed on the spindle side, through this function, also can achieve an external zero pulse stop.
Electronic gear ratio: to achieve synchronous belt drive ratio (non-1: 1) CNC machine tool processing applications.
The accuracy of reaming workpieces processing accurate stop can be accurate to 0.1 ° or less.
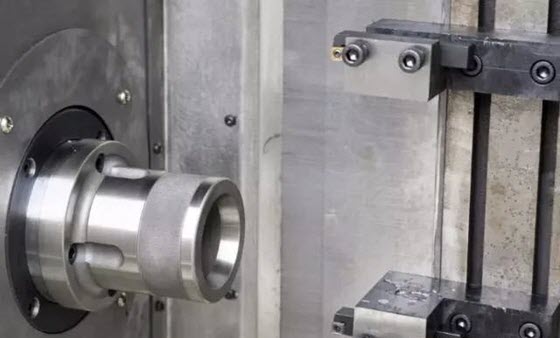
Main spindle servo