The Development History of Inverter
As an "old acquaintance" in the field of industrial control, frequency inverters have been active in various industries for decades. It bears the responsibility of motor speed regulation, and plays an indispensable role in improving production processes and energy conservation. From a professional point of view, it is actually a kind of power control equipment that uses variable frequency technology and microelectronic technology to control the speed of the AC motor by changing the frequency of the AC motor power supply.
So, what is the significance of the inverter for motor speed regulation? Why is AC motor speed control "none but it"? Regarding the importance of the frequency inverter, we will understand its birth and development process from the following aspects.
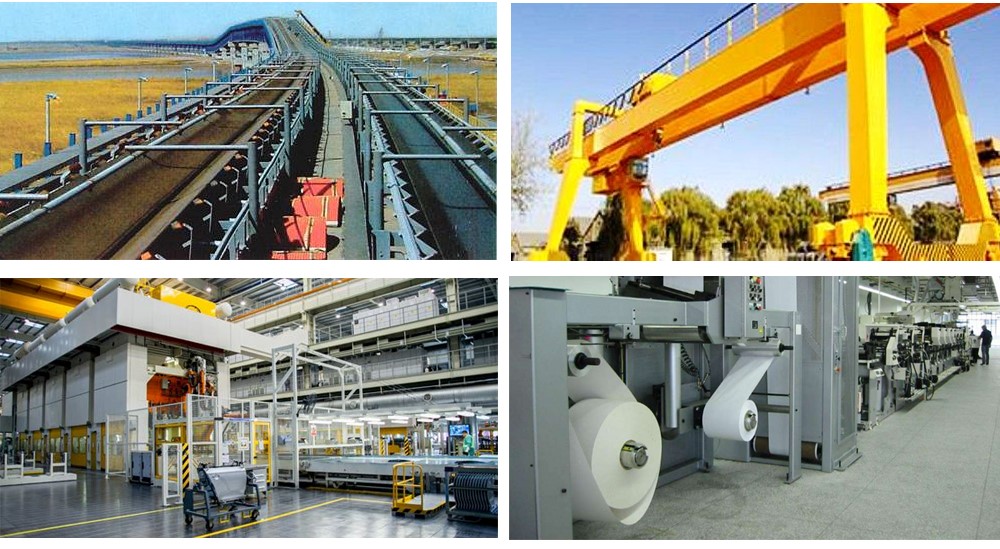
Birth and development process
The background of the era before the birth of the inverter
In industrial production, the use of motors to accurately control the speed and position of objects or components is a necessary process. For example: lifting equipment, loom equipment, material conveyor belts, rewinding and unwinding, etc., and other types of machinery and equipment.
When the motor speed control technology is still immature, people can only use some mechanical aids to solve the problem of object motion control, such as gearboxes, clutches, etc., which are not mechanically adjustable. In the case of a motor, in order to achieve a certain sporting purpose, it is necessary to replace the gearbox, change the gear ratio, or switch the clutch. This process is not only very time consuming, but also a great loss to the machine.
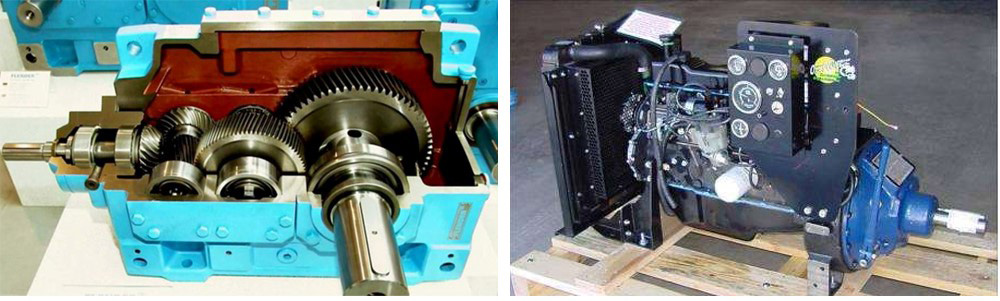
The use of motors to accurately control the speed and position of objects or components is a necessary process
In another type of fluid control application scenario, the motor drives the impeller to rotate, thereby propelling gas or liquid flow or generating corresponding gas and hydraulic pressure. In the early stage, the motor speed cannot be freely controlled, the control of fluid flow and pressure can only be achieved by opening and closing the valve in the pipeline, which is a waste of electrical energy.
In the age when there is no frequency inverter, because the motor speed cannot be adjusted freely, in order to achieve certain motion purposes, the traditional machine has to add many accessories, which not only increases the overall system complexity and cost, but also limits the performance and development space of the device, in order to solve these problems, the introduction of simple and efficient motor speed control technology has been a hot spot and pain point of industrial transmission research.
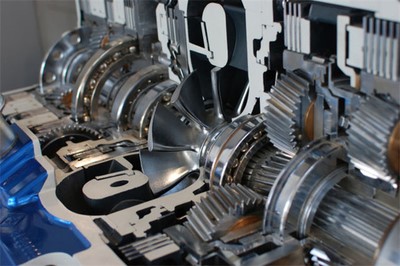
In the age when there is no frequency inverter
Dilemma in motor speed regulation
The focus of early motor speed regulation has always been DC motor. One of the main reasons is that people first grasp the rectification technology, and the mechanical characteristics of DC motor are also very suitable for certain scenes. The simplest way to adjust the armature voltage is to string resistors. The higher the resistance is, the greater the voltage drops, and the slower the DC motor speed would be.
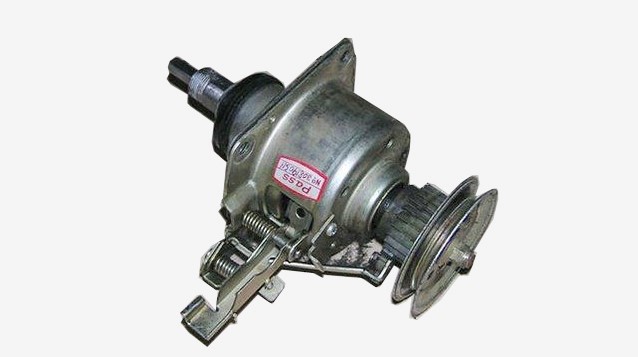
The higher the resistance is, the greater the voltage drop
However, the defects of the DC motor are also very obvious. For example, the collector ring and the carbon brush require regular maintenance, the DC motor manufacturing process is complicated, and the manufacturing cost is high. This means that DC motors are not suitable for a wide range of motor applications.
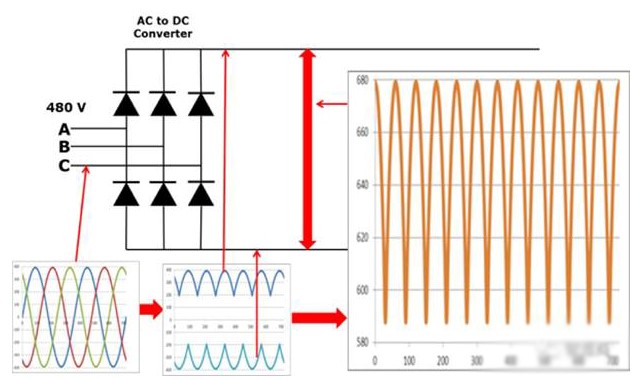
DC motors are not suitable for a wide range of motor applications
Compared with DC motors, AC motors are much simpler in internal structure, without commutator and other structures. They are easy to manufacture and stable, suitable for high-speed, high-voltage, high-current applications. The only thing that needs to be solved is the control problem of AC motor speed.
Evolution of the frequency inverter
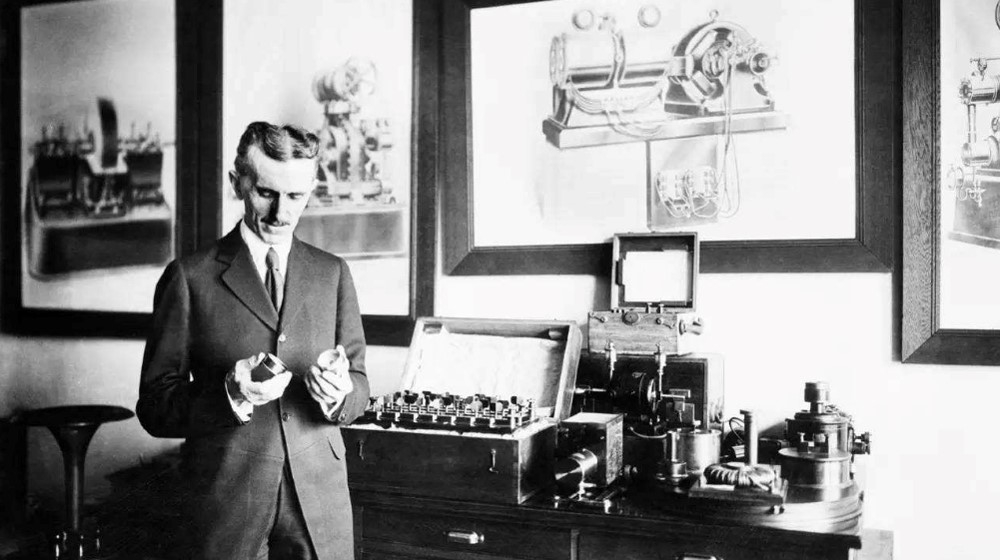
Nikola Tesla invents AC motor
In 1888, AC and AC motors were introduced, but after a long time, AC motors were only able to operate at one or more fixed speeds due to their structural reasons. Its speed is proportional to the frequency and inversely proportional to the number of pole-pairs.
n = 60 f( 1 - s )/ p
It can be seen from the above formula that the slip rate “s” and the pole pair “p” are the inherent characteristic parameters of the motor. It cannot be changed after the motor is manufactured. If you want to adjust the speed freely, only change the input frequency of its power supply “f”. There is basically no means to freely adjust the frequency of the grid voltage before the birth of the inverter.
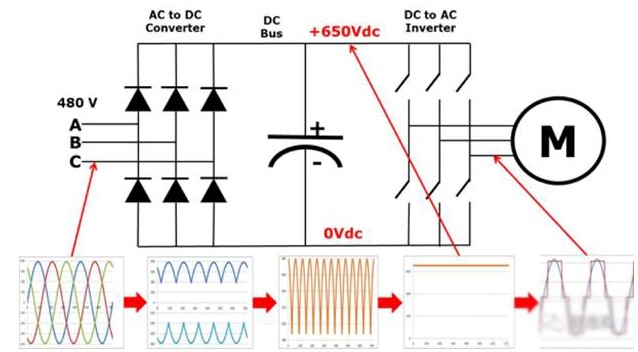
The slip rate “s” and the pole pair “p” are the inherent characteristic parameters of the motor
In the 1980s, with the development of semiconductor technology, especially microprocessors and thyristors, microprocessors have been used to control the conduction state of thyristors. In this way, the microprocessor can be used to control the conduction closing of the upper and lower bridge switching elements, and the continuous operation can be performed according to a specific timing, so that the direct current can be converted into alternating current, which is what we often call the inverter technology; At the same time, we can adjust the operating cycle of the power component to open and close, that means the adjustment of the inverter output frequency can be realized.
Finally, combined with rectification technology, we can quickly convert the standard frequency of the grid into the corresponding frequency and the AC of the corresponding voltage according to the amplitude and frequency of the required power supply, thereby changing the input frequency of the motor to realize the adjustment control of the speed of the AC motor. After a long period of technological development and unremitting efforts of scientists, the frequency inverter has been upgraded and evolved in one application, and it has gradually become what we see today.
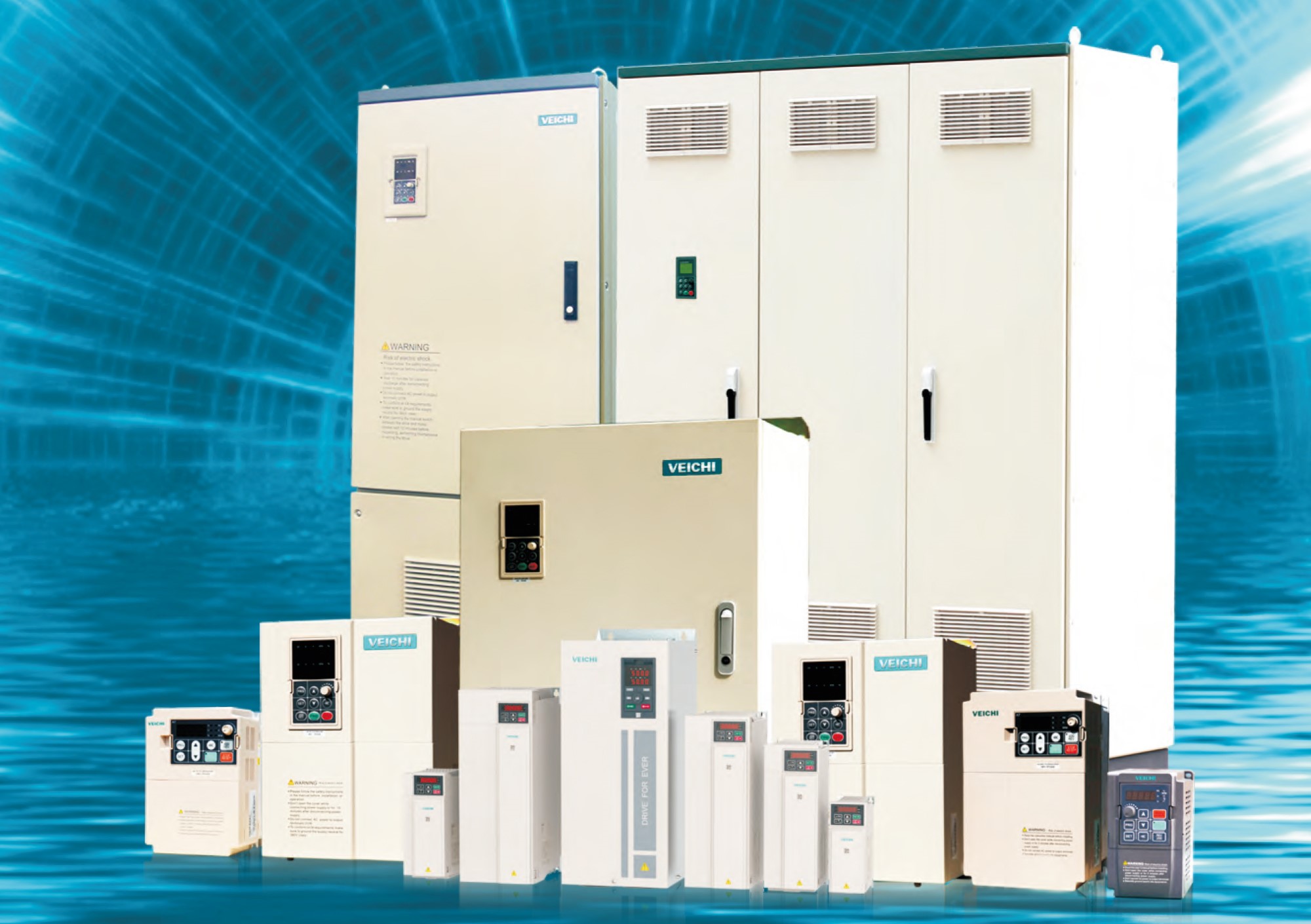
VEICHI products
Let’s understand the development of the inverter from the beginning, and then introduce the development of the frequency conversion technology. It summed up can basically be divided into the following three stages.
1. Replacement of power electronics
With the continuous development of semiconductor devices, we use a fully-controlled device instead of a semi-controlled thyristor (SCR) to change the output waveform into a pulse-width modulated PWM waveform, which greatly reduces the harmonic components, the speed range of the asynchronous motor is increased, and the torque fluctuation is reduced.
The operating frequency of the IGBT can generally reach between 10 and 20 kHz. Compared with the BJT of the triode BJT, the operating frequency is an order of magnitude higher, especially in terms of some voltage and current indicators, which have exceeded the use of BJT, such as current surge tolerance, voltage blocking peak and so on. Due to the use of IGBTs, the carrier frequency can be increased and even the required PWM waveform can be formed, which can greatly reduce harmonic noise. Therefore, in current inverter applications, IGBT has basically replaced BJT.
IPM is the intelligent power module; it uses IGBT as the switching device, which not only integrates the power switching device and the driving circuit. It also integrates fault detection circuits such as overvoltage, overcurrent and overheating, and can send detection signals to the CPU. Even if a load accident or improper use occurs, the IPM itself can be guaranteed to be free from damage.
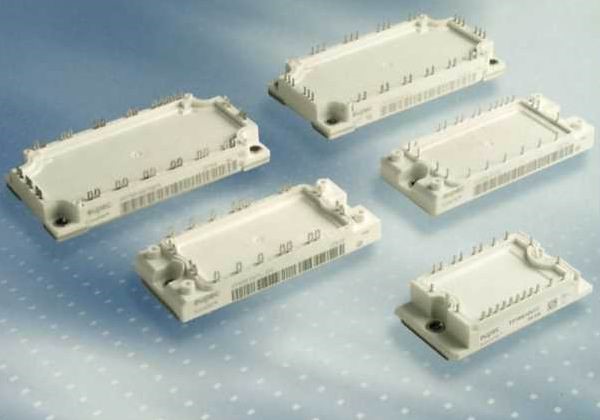
IGBT module
2. Development of control methods
The previous inverter control method adopted the constant voltage ratio that is V/f control. V is the effective value of the voltage. Changing V/f can only adjust the steady-state flux and torque of the motor. In order to improve the torque under low frequency conditions, torque boosting is required. Usually, the voltage is compensated, and some can compensate the stator winding voltage drop with load changes.
Later, the inverter appeared a new control method - vector control. Its basic principle is to establish a model of the equivalent DC motor, and the stator current of the asynchronous machine is decomposed into the excitation component and the torque component separately. Controlling the excitation vector is the most important, so the vector control is called the field oriented control, and the torque control is indirect.
Vector control system structure diagramVector control requires coordinate transformation operations and the need to detect the actual speed signal, so the speed sensor is required for feedback that is closed loop vector control. Then, a vector scheme of speed sensorless vector control is proposed, which is calculated based on the phase voltage and phase current of the actual running of the motor and the parameters of the stator and rotor windings, and then the observation values of the rotor flux and torque current are calculated, thereby realizing the vector control of the field oriented.
Another way to develop in parallel with vector control is called Direct Torque Control (DTC), which emphasizes direct control of torque. The method is based on the measured motor voltage and current to calculate the estimated value of the motor flux and torque, and after controlling the torque, the speed of the motor can also be controlled.
3. Functional diversification
The current frequency inverter relies on a very powerful microprocessor, in addition to the basic tasks of the motor frequency conversion speed regulation, there are also a variety of built-in functions. E.g:
(1) Automatic acceleration and deceleration.
(2) The program runs.
(3) Automatic energy saving operation.
(4) Motor parameter self-learning.
(5) PID control operation.
(6) Communication and feedback functions.
In the 1970s, Siemens engineers first proposed the theory of asynchronous motor vector control to solve the problem of AC motor torque control. For direct torque control, the general literature believed that it was taught by Professor M. Depenbrock of Ruhr University and I.Takahashi of Japan was proposed separately in 1985. It can be seen that the research results of motor control in foreign countries are earlier than those in China, and their inverter products are also entering the public's field of vision before our domestic brands.
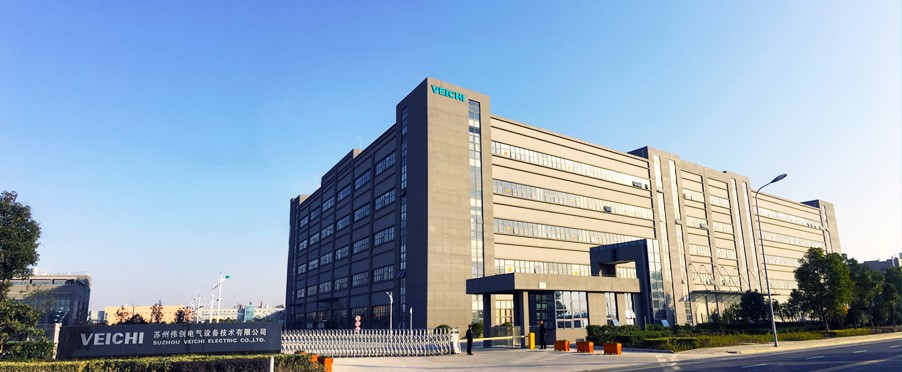
VEICHI
Now, with the continuous learning and research of many engineers in this field in China, the domestic inverter industry, in terms of brand, performance, and price, has largely satisfied the development status of China's industry. As a company specializing in R&D, production and service of frequency inverters, VEICHI has been focusing on research in this field, and carefully manufactures each frequency inversion product to contribute to the future of intelligent manufacturing 2025.